Rapid production lines have revolutionized the food processing and pharmaceutical industries, allowing producers to minimize costs while increasing profit margins. While this is excellent news for the industry, speed should never precede food safety. To avoid this, a fast and accurate metal detector in food processing has never been more critical. Here are some pointers to help you choose a decent and economical metal detector.
Your Product’s Characteristics
Numerous varieties of metal detectors are available, each tailored specifically to a specific merchandise category. For instance, a metal detector suited for use with a salmon fillet line will be different from gravity feed metal detectors necessary for use with granules, powders, or other types of loose materials. Another essential element to consider is the state of the product being examined, which might be either dry or moist. For this reason, it is necessary to consider the characteristics of the products produced by your line. These characteristics should include variations in product kind and temperature and differences in product size.
Budget
While shopping for a metal detector, price is crucial. A metal detector’s high price does not always indicate its quality. Therefore, while the price is essential, the quality of the instruments should be given equal consideration. A metal detector can be purchased for a reasonable price without sacrificing quality. Look out for the well-known brand’s price tag, as it may have been inflated to reflect the premium status of the brand’s name. Choose a metal detector within your budget by researching the market and reading reviews from the previous customers to gain insight into what you are buying exactly.
Function
Many different kinds of metal detection systems are used on production lines. Metal detection needs might also vary widely along a single manufacturing line. For instance, a product’s packing line may require ultra-high metal detection sensitivity during the last stages of production before it is distributed to customers. On the other hand, early-stage metal detectors may not require such high sensitivity levels because their primary duty will be to protect equipment, i.e., by identifying particles of metal that are large enough to damage production line equipment. As a result, you should look for a metal detector that meets the sensitivity standards of your manufacturing line and quality control procedures. It is common practice to test the machine’s sensitivity to various metals and to make sure it can identify magnetic and non-magnetic materials, such as stainless steel.
Check Detection and Inspection Challenges
Metal detecting technology is not always sensitive enough to avoid false triggering, resulting in unnecessary waste, slowed production, and reduced revenues. Conventional metal detectors may struggle to identify metals correctly and consistently in production lines. This is because various products emit distinct signals due to differences in moisture content, known as the product effect. This problem can be solved by using multispectral x-ray detectors. Another difficulty is maximizing efficiency while retaining robust metal detecting systems. No company wants to slow down its food production lines. But, they must balance speed and accuracy to identify potential food safety issues and prevent costly recalls and reputational harm. Operator safety is critical. Accidents are distressing for the individual(s) involved, their families, and their coworkers. They always lead to downtime; if word gets out, it could damage your company’s image. To ensure the safety of workers, the metal detection system you select requires careful consideration of every aspect of its design. When deciding on a metal detecting system, evaluate if it features shatterproof round-edge guards, safety valves, and guarded in-feed and out-feed rollers to eliminate the chance of finger traps. You must also provide adequate training. It is critical for operator safety that people using machines follow manufacturer guidelines.
Competencies for Machine Learning
Each manufacturing facility and its output are one-of-a-kind. Hence, it is impossible to attain the highest levels of contaminant detection precision using specified parameters. One must select a metal detector with machine-learning features to solve this problem. A metal detector’s auto-learn system is the name given to this function by some manufacturers. During initial setup, items are fed through the metal detector so that the auto-learn system can determine the optimal detection sensitivity, considering the product’s characteristics and the line’s speed. That is to say, the metal detector’s built-in machine-learning capabilities adjust the settings automatically. If you sell more than one kind of product, you may start the procedure over. Another convenient option has the auto-learn system on a metal detector running in the background during regular line operation. The data generated during this learning phase can be analyzed to unearth new optimization opportunities, increasing the machine’s accuracy.
Location of the Metal Detector Conditions
Another crucial factor is where the metal detector will be placed. The wetness or dryness of the inspection area, the possibility of temperature shifts, and the cleaning methods on your production line are all crucial elements to consider. For instance, metal detectors with a lower rating can withstand low-pressure washdowns commonly used in cleaning procedures. A metal detector with a higher rating is necessary if your cleaning methods include high water temperatures and pressures.
Maintenance
Your equipment needs regular, professional servicing for the best performance and longest possible lifespan. Preventative maintenance on machinery guarantees that any impending mechanical or electrical issues can be fixed far before a breakdown. To make the most informed decision possible for your food processing and packaging lines, you must examine your product thoroughly, the food processing environment, and specialists’ advice. To guarantee the highest performance of your metal detection and x-ray inspection systems, you must follow a few basic steps. Begin by ensuring that it is installed according to the manufacturer’s standards as well as performing regular surveillance checks. Additionally, make sure to clean these tools regularly in accordance with what’s recommended by their maker and keep an inventory of replacement components ready at all times for when necessary maintenance needs arise.
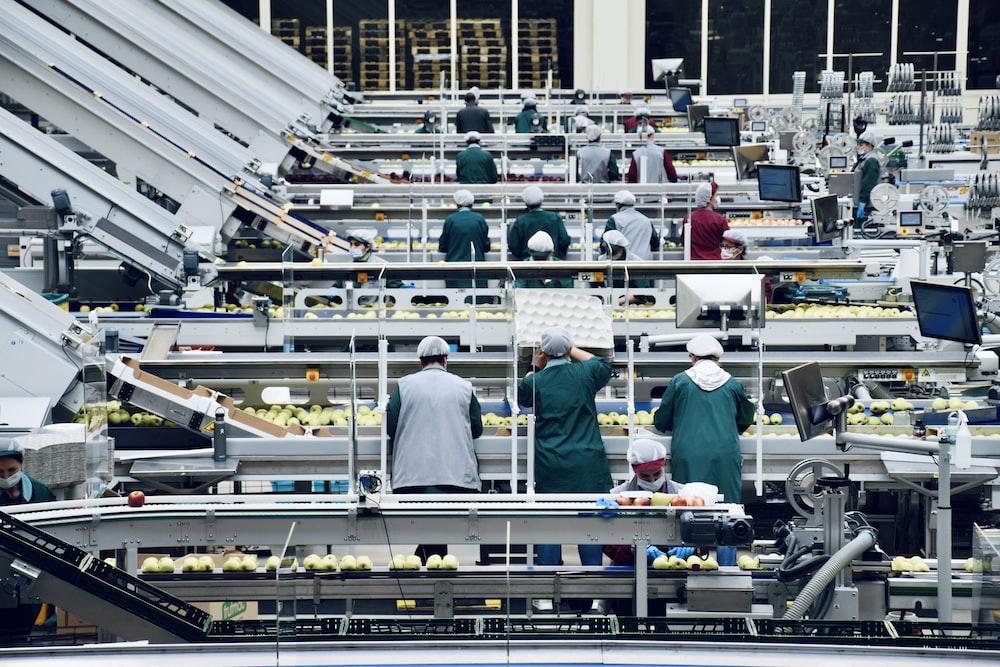
Metal detection is a critical step to ensure contaminants are not present in the food production process. To assist the food industry make an informed decision, new technologies come with a comprehensive checklist that factors in product, application, and budget when selecting an inspection system. It’s important to weigh both operational expenses against capital expenditure while evaluating the expected service life of various units before making any decisions. Don’t let increases in production capacity and machine dependability slip your mind. If you need that extra oomph later, think about investing in a machine with fewer upgrade requirements now.